Our guide to packaging line automation offers a visual overview of what a manual, semi-automated and fully automated packaging line could look like. What emerges is a direct correlation between the level of automation and the number of workers required along the line; a manual line requires a larger workforce to carry out tasks and quality assurance processes in comparison to semi or fully automated lines.
In a manual packaging environment, you would typically have a minimum of 3 people completing the process of box erecting, packing, sealing, labelling and palletising. Operating in a confined space has been a problem during the pandemic and social distancing guidelines have forced manufacturers to rethink processes and automate where possible or they drastically reduce the speed of throughput and slow down production.
Social distancing may have been a strong catalyst for packaging automation however there is a constellation of benefits way beyond spacing out your workforce, including increased productivity, efficiency and accuracy. When automating, even in a partial way, you are redeploying workers away from the packaging line and it is important to consider that there are a reduced number of eyes on the line. We want to explain how barcode verification and validation can be utilised as you move towards your automation goals to safeguard your business from errors causing downtime and ultimately your reputation.
First, let us look at the distinction between verification and validation in the world of barcodes. Barcodes are used in almost every manufacturing environment and are pretty much integral to any type of automatic data capture operations. The packaging line is no exception. Without barcodes, manufacturers would find their whole operations slow right down and level of accuracy within operations deteriorate dramatically.
Barcode verification and validation are terms that are often confused, so let us clear that up first. Barcode verification is the process of confirming the print quality of a barcode and ensuring it meets ISO/ANSI standards. Barcode validation ensures that the correct barcode information is being placed on the correct product. It is important that verification and validation work together, otherwise you may end up with the situation where a label passes a validation test but is not up to scratch on print quality, compromising your business. Preventing incorrect or poor-quality bar codes from entering the supply chain eliminates fines, rejects and rework for suppliers.
Image of barcode verification taken from one of our packaging lines
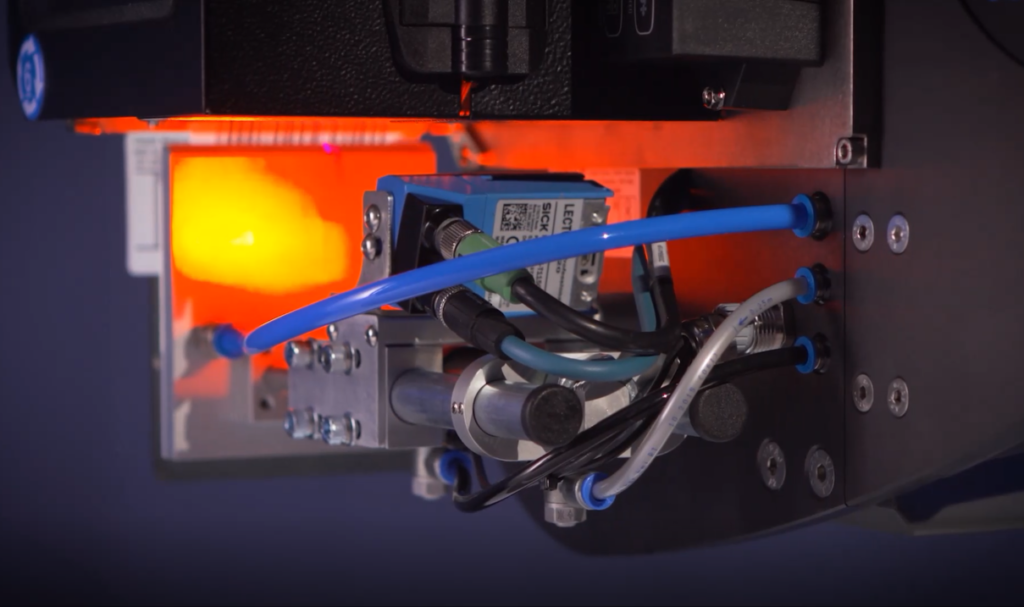
It is the manufacturers’ responsibility to ensure that bar code formats satisfy the requirements of International Standard ISO/IEC 15416, and are compliant with the GS1UK Coding System. ISO/IEC 15416 requires 7 attributes to be tested in 10 separate positions of each barcode. The tested attributes are:
- Decode – checks that the area being scanned meets the criteria of a recognized bar code format.
- Minimum reflectance – compares the reflectance of the bar to that of the background.
- Symbol contrast – measures the overall range of contrast between the bars and the background media.
- Minimum edge contrast – measures the definition of the poorest bar in the code.
- Modulation – measures the consistency of reflectance throughout.
- Defects – ensures bars are complete and spaces are empty.
- Decodability – measures the dimensional accuracy of the bar code.
Phew! As you can see, the expectations are high and if done by sight on a manual basis, the margin for error is high as well as being a rigorous, time consuming process. The quality of the sampling method and the speed of interpretation of results is critical to implementing an effective procedure to capture early failures and react before production, packing and distribution have been executed.
This process is extensive and time consuming when carried out manually, however it’s a critical part of the packaging process to ensure compliance to a uniform standard and clients will be asking for evidence of these rigorous procedures. If you’re reliant on a manual verification and validation process, you leave yourself open to human error and slow down your productivity.
Verification and validation is usually considered for one of two reasons – either a customer insists, or they put it in place because they have encountered quality issues in the past. It is far better to implement verification and validation as part of the whole automation process from the outset than risk business reputation or penalties, and with a strong return on investment promise coupled with the argument for best practise it should be worth exploring in any packaging line environment.
In a semi-automated environment, it may be that barcode checking is carried out via inline scanning equipment, or that barcode inspection can be carried out through the intelligent capabilities of more advanced scanning devices. Using either of these mechanisms will boost accuracy.
In a fully automated packaging line environment, a system like Cobalt Sentinel can be incorporated into a larger solution, where it applies additional interpretive logic to more basic scanning devices. The benefits of this include full, in-line verification resulting in an ‘ANSI equivalent’ grading of A-D or Fail, degradation of quality is identified and displayed on screen from its earliest stage, plus line operatives are fully aware of the severity of the degradation and can make informed decisions on the corrective action required to continually achieve the highest quality ratings.
However, a good quality barcode is worthless if it incorrectly identifies pack contents. Validity checks ensure the barcode on outer packaging truly reflects the actual product content. Fully automated validation can deliver match code functionality to check pre-printed media, off-line printed labels and in-line coding, validated against pre-defined packaging requirements before the packing process begins. This coding coordination ensures 100% validation of primary and secondary packaging to actual contents.
As we have discussed, verifying and validating barcode labels is a complex business! Automating this part of the packaging process it is worth considering, even if you plan to continue printing and applying the labels manually. However, the value of an integrated solution, incorporating box erecting, case sealing and print and apply barcode labelling with validation and verification onboard will give you the full benefits of automation while ensuring full quality compliance.