Machine vision combines computer science and engineering and involves the ability of machines to interpret and understand visual information captured in a controlled environment. It employs hardware and software to capture and process images, allowing machines to make decisions and perform subsequent tasks based on what they “see”.
This guide explores Machine Vision, how it works, and its role in Manufacturing.
- Machine Vision and its use in Manufacturing
- How Machine Vision Works
- Examples of Machine Vision Applications
- Machine Vision Misconception Mythbusting
A PDF version of our Machine Vision guide is also available to download at the bottom of the page.
What is Machine Vision, and how is it used in Manufacturing?
Machine vision has much to offer in a manufacturing or processing environment. It can be used to read text, inspect components on an assembly line, identify quality control issues in packaging or labelling, predict maintenance schedules and much more besides.
Often, these are tasks carried out by a person and, given the work’s repetitive, mundane (or overly complex) nature, are prone to error. And errors on a production line mean lost revenue – whether caused by reworking faulty products, goods rejected by customers thanks to faulty packaging or spoiled goods; it’s never a good thing.
Machine vision can help reduce many of these issues, but for many manufacturers, machine vision often strikes a note of terror. It’s perceived as too cutting-edge, hard to implement, expensive and, quite frankly, too much of a stretch for most production lines.
But those perceptions are largely false. The technology is far from new and harks back to the late 1950s when scientists first theorised that a computer could see images, recognise them and interpret information based on what it could see.
Although the hardware and software were not available to make this a reality until the 1970s, the theory held water. By the 1980s, algorithms for pattern recognition, object detection and image processing had been developed for industrial applications.
The next two decades saw incredible advances in two related fields: robotics and digital imaging. The former could be instructed to act on what machine vision systems saw. As digital imaging became more commonplace, the quality of images increased, as did the speed with which images could be interpreted by corresponding software.
The final piece in the puzzle was the prevalence of deep learning and AI, which allowed machine vision software to reference huge data sets to help in decision-making. Now, almost a quarter of a way through the 21st century, machine vision has finally come of age. Equipment costs are lower than ever, software is more advanced than ever, and ease of set-up makes machine vision accessible for almost any manufacturing scenario.
In recent years, real advancements have come in the brain behind vision–image processing. Here, the magic happens through machine learning, a concept where machines learn patterns and make decisions. Improvements in machine learning have propelled machine vision forward, allowing systems to analyse images more accurately and faster than ever before.
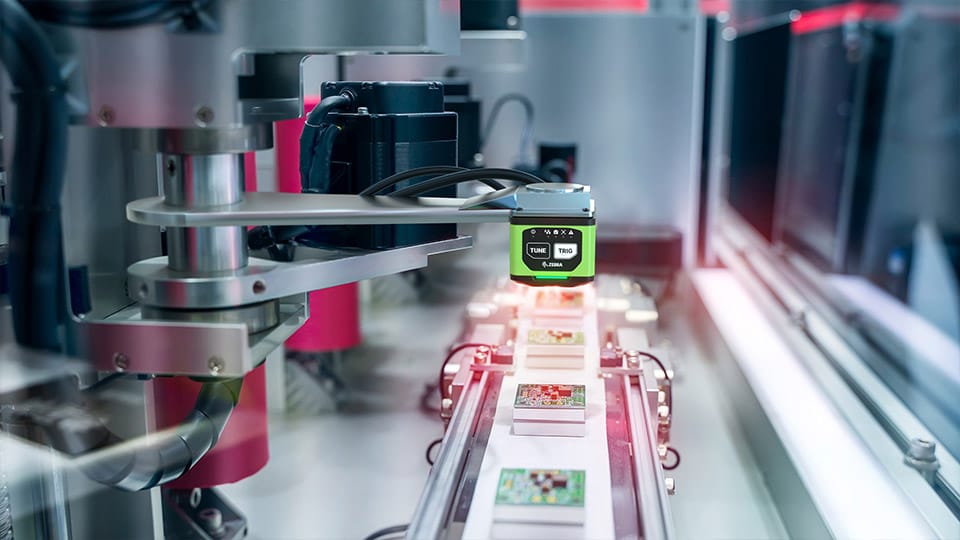
How Does Machine Vision Work?
The key components of a machine vision system involve cameras for image capture, software for image processing and analysis, hardware to integrate these elements, and other equipment to perform tasks. Let’s break down each element in more detail.
Image Capture
Modern machine vision systems use digital cameras to capture high-resolution images of the objects or scenes they inspect. These cameras have sensors that convert light into electronic signals, forming a digital representation of the visual input. Additional lighting or specific lens types may be required to ensure the clarity of images, depending on the situation.
Improvements in camera technology, including higher resolutions, faster frame rates, and enhanced sensitivity, have significantly boosted the accuracy and speed of image capture, with each new iteration of machine vision camera getting better and better. Highly advanced systems can now utilise thermal imaging, ultraviolet or 3D cameras for specialist applications.
Image Processing
Once the images are captured, machine vision systems use image pre-processing techniques to make the image as good as possible for analysis. Image pre-processing involves noise reduction (which removes the grainy look that digital images get when taken in low light) and contrast enhancement.
The second stage in image processing is segmentation and/or feature extraction. Both stages can be used together but don’t have to be.
Segmentation involves dividing an image into different regions or segments based on certain characteristics such as colour, intensity or texture. It aims to simplify the image into something more meaningful and easier to analyse.
Feature extraction involves identifying and extracting specific features or patterns from an image or part of a segmented image, such as edges, corners or text. These detailed features and how they compare to what the system understands to be “correct” determine the next steps the item will take in production.
For example, imagine a circuit board that is made up of dozens of components. A machine vision system could be employed to inspect each board as it passes along a production line, “split” the areas of the board into segments, and then extract relevant features to begin analysis per segment. Any specific production issues could then be flagged up and resolved.
Analysis and Action
The processed images are then subjected to further examination and interpretation. This is where the machine vision system makes decisions based on predefined criteria or learned patterns.
For instance, in the quality control example of the circuit board, the system might identify a component in the wrong place, the wrong colour or missing altogether, all by comparing the captured images to a standard reference, learnt as part of deep learning setup.
Armed with this information, machine vision software can be integrated with other software and hardware features to trigger certain actions. This could be as simple as a warning beacon to alert operators to an issue, or it might trigger the production line to stop or divert that item into a separate stream for remediation. In very advanced assembly process automation, it might even guide robotic arms based on the visual input to correct the placement of components.
In short, the options for the next actions are limited only by imagination and budget. But the speed and accuracy with which decisions can be made thanks to a machine vision system make this a very real possibility.
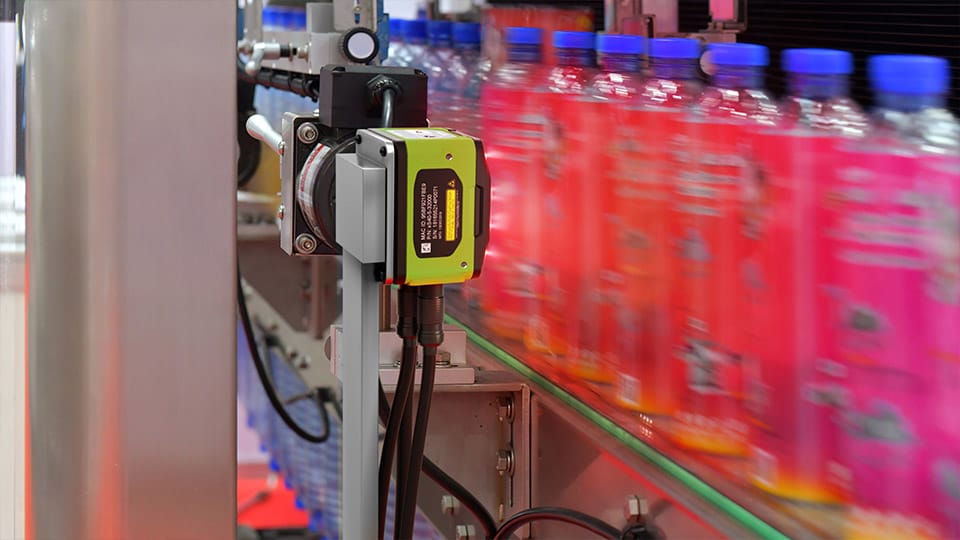
Examples of Machine Vision Applications
With a good understanding of how machine vision works, let’s look at where the technology is making an impact in real-life examples:
- In manufacturing, machine vision can be an eagle-eyed quality control agent, far more capable and consistent than the human eye.
- In packaging standards, machine vision can spot errors and issues and prevent wrongly packaged items from ever being shipped out.
- In assembly production, machine vision can ensure every item is correctly fitted in the right place and orientation every time.
Here are just a couple of examples of how machine vision can help SME manufacturers:
Quality Control
Imagine a bustling manufacturing line producing complex electrical components. Here, machine vision utilises segmentation and feature extraction to isolate areas for inspection and subsequently detect potential defects, always ensuring that the right components are in the right place.
As the item moves down the assembly line, the machine vision system captures detailed images, examining every nook and cranny. It’s looking for imperfections like scratches, misalignments, or faulty components that could slip past the human eye.
If a flaw is detected, the system can swiftly trigger an alert, signalling for immediate attention. This meticulous quality control ensures that each item that rolls off the line meets the highest standards, providing customers with fit-for-purpose products and reducing the likelihood of defects reaching the market.
Packaging Inspection
In a packaging inspection role, machine vision ensures that every product that is deemed acceptable is wrapped, packed and labelled flawlessly.
Imagine a food production facility handling and packaging perishable salad leaves into wrap bags. If one piece of lettuce doesn’t enter the bag and breaks the seal, the whole bag can be spoiled. That single bag can cause an entire shipment to be rejected by the end customer, causing a massive knock-on effect in terms of lost time, destroyed products, shipping costs that can’t be reclaimed and more. All because nobody spotted a piece of lettuce in the wrong place.
Machine vision is perfectly placed to deal with this scenario, diligently monitoring the bags being filled and sealed and rejecting unsafe bags to ensure the whole batch is always safe.
Compliance Monitoring
In compliance monitoring, machine vision ensures businesses can adhere to regulatory standards and safety requirements without hiring multiple staff in different shifts to monitor things by hand.
In an environment where compliance standards drive what is considered acceptable – for example, a pharmaceutical setting, machine vision is incredibly helpful. Imagine a scenario where tablets or pills must be packaged in a fixed quantity and then correctly labelled to be compliant.
Machine vision can examine each tablet as it progresses down the conveyor belt, checking for damage, quantities, accurate labels, properly sealed bottles, or any other signs of damage.
If anything is compromised, the machine vision system immediately flags it for corrective action.
Reading text or barcodes (character recognition)
In an environment where date codes are applied to packaging, it’s vital to know that the information is correctly applied each time and is legible to the human eye.
Machine vision excels in such an environment. Modern software can easily recognise the date, batch and other relevant information for FMCG and perishable goods to ensure the right information is applied to packaging.
Taking this a step further, if the information on a package is outside a particular batch’s scope, an item can be rejected, and action can be taken to remove it from the production line, ensuring goods remain consistent and high quality throughout the supply chain.
Assembly Process Automation
Machine vision can revolutionise the efficiency of putting together complex products. Imagine an automotive assembly line with components moving rapidly down the conveyor belt. Machine vision takes charge, analysing each part with precision as it arrives.
In this scenario, the system can guide robotic arms to perform intricate tasks, such as precisely placing bolts or attaching components, and not just the same repetitive process repeatedly. Each interaction can be different. The machine vision system ensures that every step in the assembly process is flawlessly executed, minimising the risk of errors and optimising production speed.
But machine vision in assembly processes doesn’t need to be as complex as controlling robotic arms. Machine Vision can ensure the systems run smoothly in smaller firms by checking goods at each stage. By automating these tasks, assembly process automation with machine vision enhances accuracy and boosts productivity, allowing manufacturers to create high-quality products faster.
Predictive Maintenance Alerting
One area that is almost an offshoot of a machine vision system is the ability to predict when machine maintenance is required. Take a situation where hundreds of components per day are made on a production line. If the failure rate of that component increases beyond normal standards, then it is highly likely that the machine responsible for that manufacturing element will also fail.
Thus, monitoring throughput quality provides an opportunity to stop bad products from being despatched and to identify and resolve the manufacturing fault responsible for the issue.
Machine Vision Misconception Mythbusting
As stated at the very start of this post, there are a lot of misconceptions about machine vision:
“They cost too much”… “The technology isn’t up to it”…“They take days to set up or reconfigure”… “They’re just not worth the investment”…
10 – 20 years ago, at least some of those statements were justified; now, that’s simply not the case.
In terms of cost, an entry-level machine vision system is not expensive. While it’s hard to put exact figures on a theoretical system, if the goal of machine vision is to check the sell-by date and code on every box leaving your production facility, and a person is currently handling that task, it’s safe to say the ROI will be in achieved in months, not years.
As for whether the technology is up to the task, at Cobalt, we primarily use Zebra Machine Vision systems and the investment Zebra has made in this area is staggering. With a range of cameras, plug-and-play software and enhanced support, machine vision has never been better.
The same applies regarding how long it takes to set up a machine vision system. A few years ago, it would be commonplace to expect to take several days to set up a system to perform relatively simple tasks. With Zebra’s machine vision cameras and software, it takes just minutes from unboxing to being online.
From the advancements in image capture, driven by cutting-edge camera technology, to the powerful strides in image processing through to accurate analysis thanks to deep learning, we’ve glimpsed how machines are gaining the ability to see, understand and direct the visual world around them.
Instead of having multiple full-time staff responsible for quality inspection and compliance monitoring, machine vision systems can perform the tasks tirelessly and more accurately across multiple shift patterns.
For more information on how machine vision systems could boost your operations’ productivity and how they could make a real difference in your business, get in touch with the team at Cobalt.
We’re always happy to help and can’t wait to discuss what machine vision could do for you.