We were approached by a major manufacturer of allergen testing components to help solve a problem costing both time and money.
The manufacturer already runs several fully automated lines, producing large volume batches of more common allergen testing components, in this case, vials filled with assays or reagents.
But with an ever-increasing array of allergies that patients can be tested against, large volume production is not always appropriate. There is not necessarily the demand nor an acceptable product shelf life to justify fully automated production and labelling. A key issue is the time it takes to stop a line, clean it and prepare for the production of a different product.
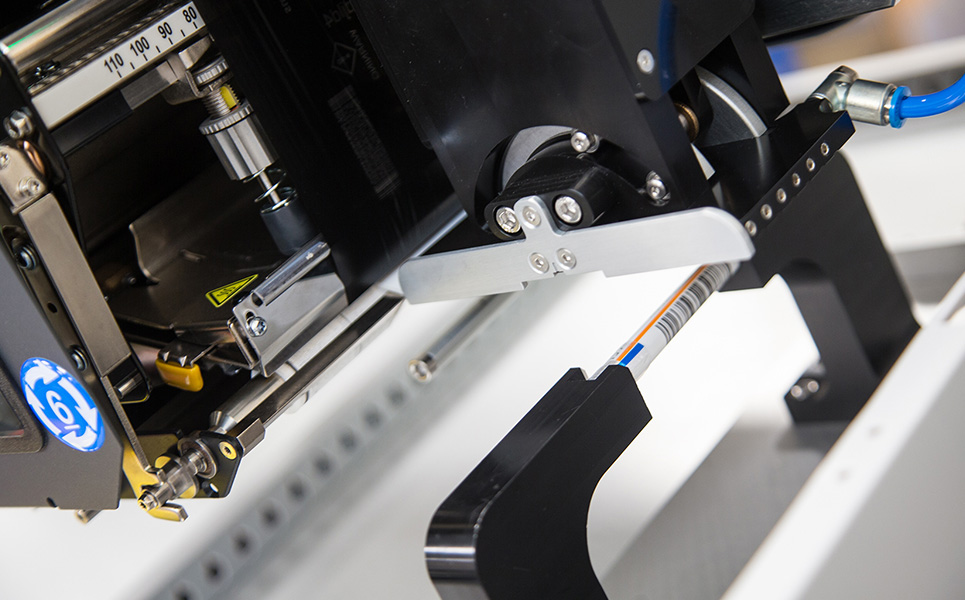
To manage the problem, we proposed an offline solution to satisfy low frequency, small batch production whilst not interfering with large volume runs and causing costly line downtime.
The solution is a two-part process which enables the application of wraparound vial labels via a semi-automated line which houses a print and apply solution. Vials are fed onto the line, which prints and wraps the contents onto a label that can be machine-read by immunology analysis laboratory equipment when testing actual patient samples.
The second label is a flag type label, applied over the machine-readable data but at a much larger size to allow operators at the testing stage to verify that the correct assays are used to carry out the appropriate patient tests.
While the flag label is critical for laboratory operators to carry out visual validation checks, it is also essential that no adhesive residue is left on the vial to impede machine reading capabilities.
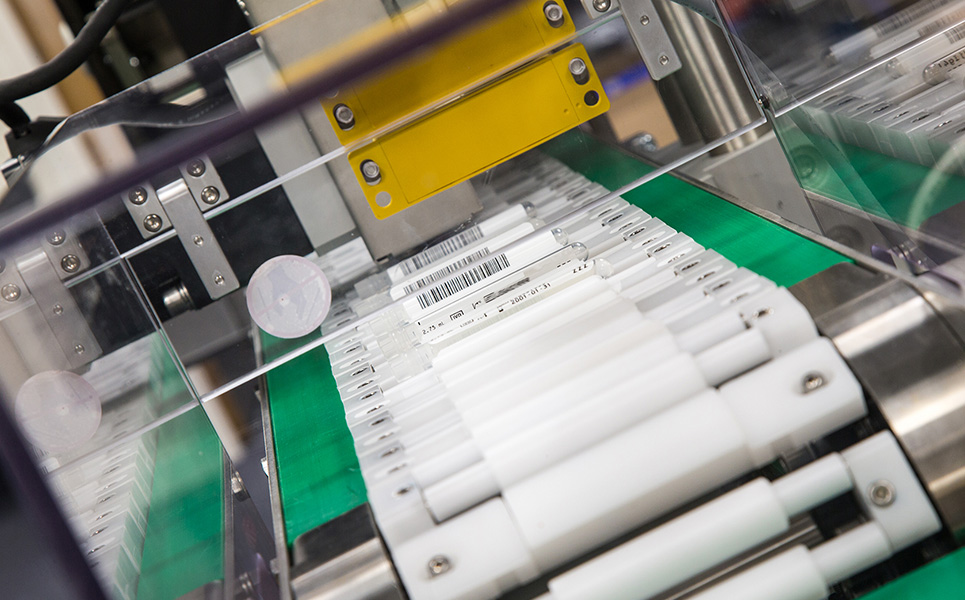
To accommodate that requirement, we designed and built a flag label applicator which supports the vial while wrapping a label around it, bringing the adhesive sides together creating a flag, with all the unique data easily readable.
The label for the machine was also designed by our in house team specifically for this project and features a central section with no adhesive in the area where the label is wrapped around the vial. The label also has a perforation to allow the operator to easily remove the flag after visual checks are complete and before tests are carried out.
The offline process meant a significant reduction in line downtime and gave the manufacturer a large degree of cost-effective flexibility for handling small volume runs.