A long-standing food manufacturing client asked us to develop automation solutions on two production lines to label pallets prior to dispatch. While such a request is not out of the ordinary for Cobalt, this particular project came with its own set of challenges.
First of all the environment the machine operates in has a colder-than-normal ambient temperature, which can cause poor label adhesion. Secondly, the machine needed to be able to apply SSCC labels at variable heights and on one or two sides of the pallet depending on the end customer.
The solution also needed to be PLC-controlled and integrated seamlessly with existing production line equipment. With a range of pallet labelling machines in our product line-up, our technical sales team specified a Nexus 20 Pallet 2 machine as the starting point for the solution.
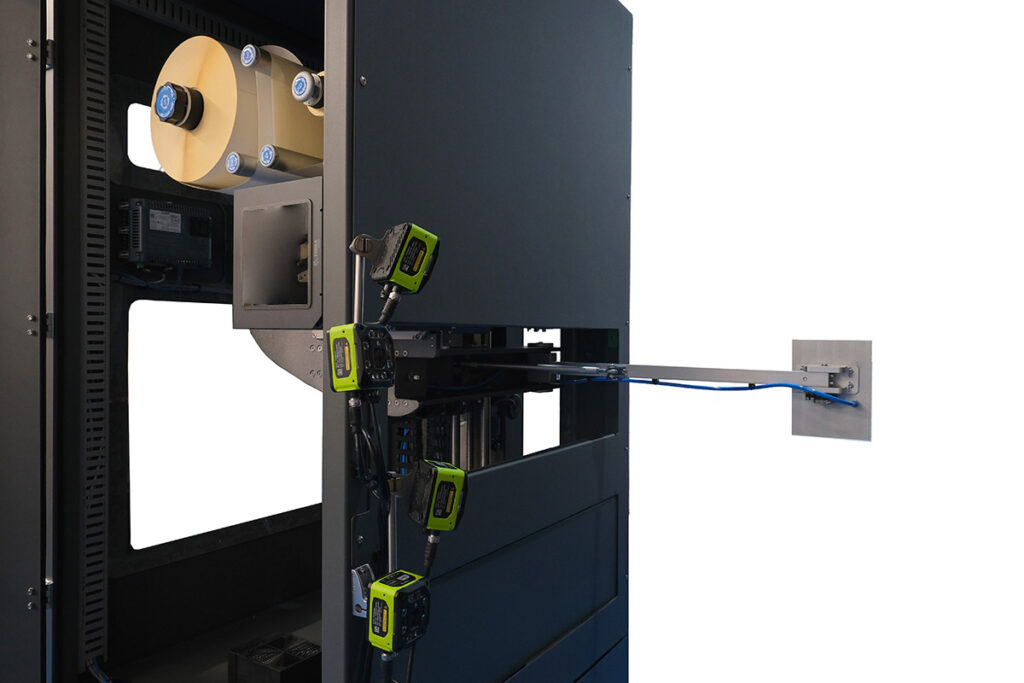
To cope with the temperatures, bespoke steel enclosures were designed along with thermostatically controlled (and also adjustable) heating fans to keep operating temperatures within the enclosure above 8°C. The enclosure itself is built around a Nexus 20 label applicator support column, and the print engine and applicator arm move up and down via an electrically driven motor to provide the variable height.
To maintain that all-important temperature, when a label is printed and the applicator arm needs to move into position to apply labels, a hydraulically operated door slides open, and on return to rest position, closes to minimise heat loss. The enclosure has two doors, one lower and one higher to allow for labelling at different heights (and to accommodate part pallets).
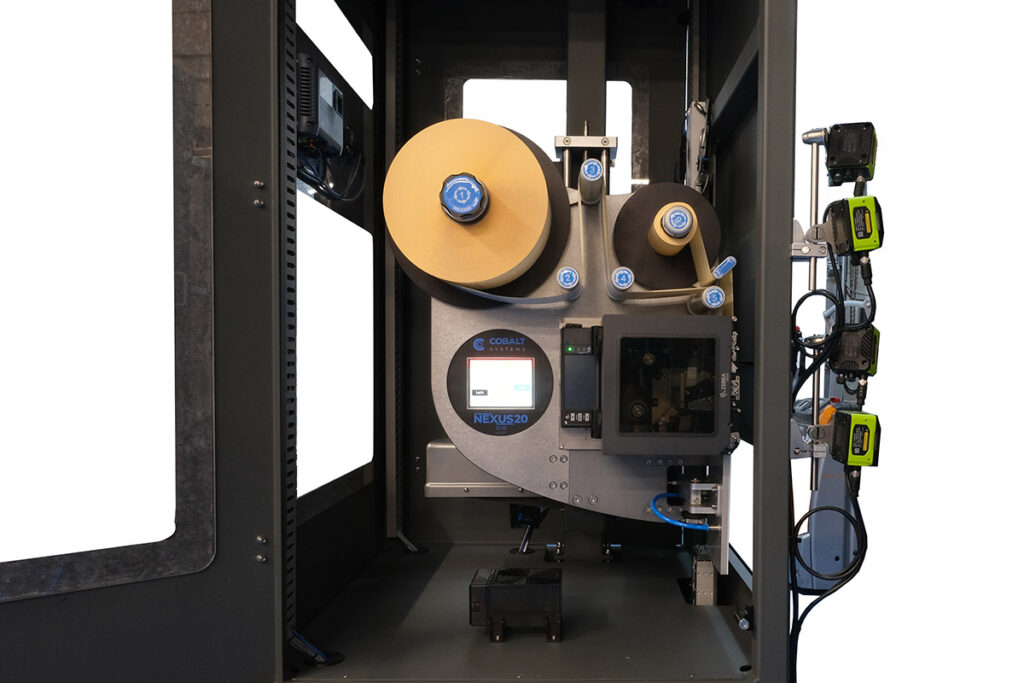
Once a label has been printed and applied, the PLC triggers one of four Zebra FS40 scanners correlating to the appropriate face and height of label application. The scanners validate the barcode’s legibility and content. If a label fails this automatic check, a second and third attempt will be made to relabel. If all of these labels fail, the line stops, and the warning beacon switches to red, alerting the operator that an issue has arisen, and manual intervention is needed to resolve the issue and reset the system.
Different customers require different labels, so the machines integrate with the existing line control PLC to ensure the correct label position. This can be either the leading face, the side of the pallet or, if required, both. Label data is generated from the customer’s ERP software, and all labels also adhere to strict SSCC requirements.
Thanks to clever industrial design, the machine’s footprint is incredibly compact and provides a reassuringly high level of safeguards for operators. As access to the machine is vital to allow for media replenishment and maintenance, the enclosure has access doors on both sides. Each is fitted with E-stop sensors to ensure the machine becomes non-functional if a door is opened.
A human-machine interface has also been built into the exterior of the enclosure so any actions taken don’t have to interrupt the machine during operation.