Choosing a print and apply solution for your business is rarely as simple as picking a machine off the shelf and including it in your production line. There are lots of factors to consider which will shape your exact requirements and help to deliver a quicker return on your investment.
This guide is Part 3 of our Guide to Print and Apply and is intended to highlight the key things to consider and to point out some pitfalls in traditional thinking.
Click here to view Part 1 – A guide to print and apply automation
Click here to view Part 2 – Choosing the right machine for your production line.
Contents
People: Operators and Engineers
It might sound like an odd first thing to consider given that a print and apply machine is intended to greatly reduce the need for human intervention…but as with any automated process, there is always some level of human resource required.
In the case of a Print and Apply solution, this means operators and engineers. Operators are typically given simple tasks like replenishing the print media when labels run out or selecting a new label when the product on the line changes.
None of these need necessarily be complicated tasks to complete, but if your operator is not very hands-on with technology or may not be a native English speaker, then simplicity is fundamental to a successful solution.
Cobalt embraces this requirement when we set to and design our machines. For example, when it comes to rethreading a roll of labels onto a spool, the threading path is labelled with numbers and arrows at each location, so it’s child’s play to follow.
Equally, our touch screen control panel uses our proprietary software which is incredibly intuitive and simple to use, plus the panel itself is built into the body of the machine where it can’t be bashed or knocked and there are no trailing wires to be caught or snagged.
From the point of view of an engineer, we know how important it is to keep a production line running. So we make our machines as robust as possible. In fact, we offer a 3 year warranty as standard to provide peace of mind.
But things go wrong and it’s important that when they do, they can be resolved quickly. Having been in the business of print and apply for over 30 years, experience tells us that when there’s a problem with a machine, in almost 90% of cases, it’s due to the print engine.
So, our machines are designed to allow your own engineer to change the print engine in less than five minutes, removing the need for costly service engineer call-outs.
Usability and Ergonomics
Still, on the subject of human interaction, there’s another consideration for a label applicator. It’s important that your operators like the machine they use. And it’s for that reason we put a lot of thinking into how our machines will be used.
For example, there are no sharp edges on the chassis or frame, so the likelihood of accidentally cutting yourself or bashing a shin or elbow is much reduced. Loading for labels is also at a sensible height so it doesn’t put unnecessary strain on the operator’s back.
As standard, our systems also come fitted with a highly visual traffic light beacon system. This is to allow operators to easily identify if a machine is running as expected, if an issue is pending or if it needs immediate attention. Coupled with that are optional siren sounders, perfect for noisy factories to grab attention.
Our belief is that if a machine is easy to use and doesn’t cause operators unnecessary aggravation, it will be treated more kindly, will therefore last longer and deliver even greater ROI.
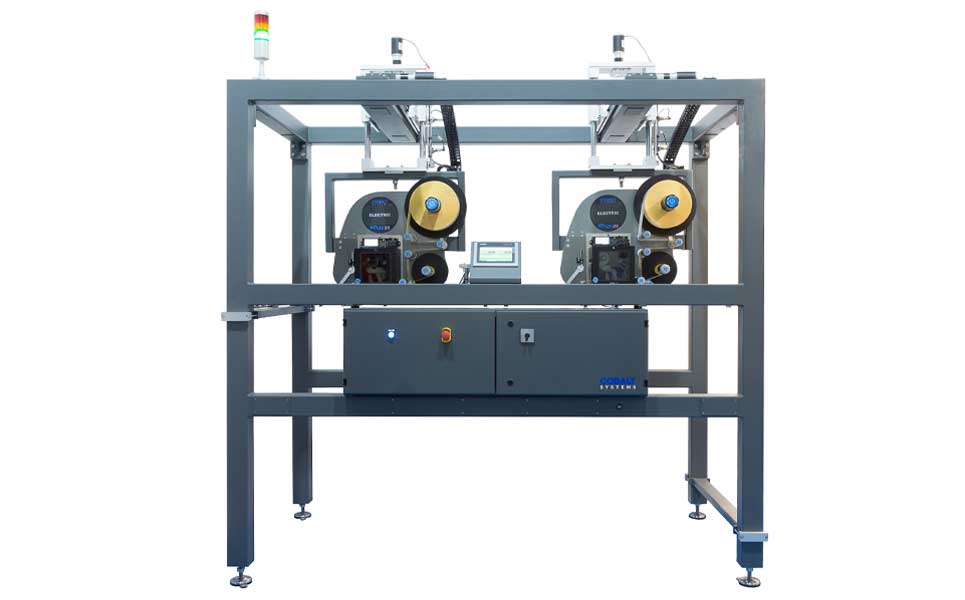
Usability and Ergonomics
Integration with Other Parts of the Production Line
It’s an unfortunate fact to acknowledge, but because barcode labelling tends to come at the end of the production line, it is often the poor cousin in terms of consideration and investment.
Which is actually a bit back to front. Because if there’s a problem with your labelling, the whole line either comes crashing to a halt or production starts to back up.
How you go about dealing with unexpected issues with your labelling process can have a huge impact on line efficiency. As standard Cobalt’s Nexus range of machine offers a Volt FREE signals configurable I/O.
This means that a signal can be sent to any other machine(s) on the production line to notify of an issue that can trigger a warning, completely pause or just slow the line down.
This removes the risk of a clogged line and mislabelled products and is built in as standard. Other machines tend to operate with a simple yes/no function and offer no nuance to enable the solution to work in tune with other elements of your production process.
Operating Environment
Manufacturing facilities differ enormously in terms of the physical environment. Some are meticulously clean and spacious, others… less so!
It’s very important to consider the following when specifying a solution:
- Will your print and apply system need an enclosure to protect it against dusty, dirty, wet, hot or cold environments?
- How much space is available to house a system?
- How much space is needed to allow for easy access to media replenishment and maintenance tasks?
It’s such an important aspect of specifying a system, but one that can be overlooked particularly if things are not as obvious as they seem.
On one occasion, a customer was experiencing difficulties with label adhesion, but only for a few hours per week in winter. It occurred when deliveries were made to the factory. Shutter doors would be left open and the temperature dropped significantly, causing the problem. An enclosure was retrofitted which solved the problem.
What about access? If you are fortunate enough to have a lot of space, this won’t be an issue, but in more confined environments, it’s good to consider how best to place and configure a machine to provide the easiest and safest setup.
A comprehensive review of where your labelling process will take place can identify requirements at the outset of a project making everything a lot smoother from the outset.
Installation and Commissioning
The level of downtime you can comfortably afford on your production line can have quite a bearing on how you go about installing a print and apply solution.
Assuming it is an existing line, then there is always going to be some level of disruption, but by considering the options at the start, it’s possible to bring this down to the very bare minimum.
The easiest way to achieve this is by opting for an integrated solution that includes a conveyor section, which can be built to size to entirely replace an existing section of your production line.
That allows for the entire operation to be built, configured and tested with live products and data before it even reaches your facility. Any issues can be ironed out ensuring a much smoother implementation and drastically reducing downtime
Software: User Access Control
Sometimes the best intentions can cause big problems. For example, when somebody with not quite enough experience or training tries to ‘do the right thing’ and ends up making it a lot worse.
That’s a common problem in a fast-moving production environment, which is why we introduced tiered User Access Control in our software solutions. It’s a configuration option that permits different user roles to make different types of adjustments.
An operator user role will only be able to stop the machine to replenish media or change the output print when switching to a new product. Whereas an admin-level user who has been appropriately trained can make wholesale changes.
Quality Control
For any manufacturer, the quality of the finished product is paramount. Nobody wants rejected goods sent back after all. That point of failure can often be traced to how products are barcoded and labelled. Incorrect, missing, badly printed or even poorly applied labels can all cause product rejections.
To counter this, your production line needs a robust and effective method to carry out two checks. The first is to see if a barcode has been printed and applied correctly and is legible. The second is to cross-check the product itself and the label to ensure it is the correct barcode.
In an ideal world, that activity needs to take place in real-time in order that any issues are identified immediately and can be dealt with.
If not, you have two serious problems to contend with: a. identifying the start point of the issue and b. rectifying it.
For example, if a large volume of finished products has been incorrectly or badly labelled, first of all, you need to know when the labels started going awry. Have ten packs or cases been affected, a hundred or even a thousand? Have any of these been shipped?
A simple way to identify and locate the first ‘bad’ label is needed so you can reapply correct labels.
When considering a print and apply solution, ask yourself what are the implications of a product being shipped with incorrect or poor labels? And how would you deal with rejected products?
Our Sentinel two-stage Validation and Verification option works across our range of Nexus Print and Appy machines and mitigates this risk entirely.
Futureproofing
A print and apply solution can be a substantial investment and to get the most out of it, it’s important to consider not just the here and now, but your future plans:
- What products might you manufacture next year or the year after?
- Will it always be on to the same finished pack or case type?
Thinking about that now can futureproof your investment by making sure you have a machine with the capability to deal with different heights, label sizes, positions and quantities.
All Cobalt machines are height adjustable by default with no need for tools. We can also configure machines to use a database-driven recipe function to automatically apply labels to different size packs or cases, triggered by proximity sensors.
The possibilities are wide-ranging but require due consideration at the outset.
Throughput, Throughput, Throughput
A large number of the factors to consider when choosing a print and apply system centre on how much you can afford downtime on your line and the knock-on effect on throughput.
Whether that’s caused by low operator skill level, incorrectly labelled product, unscheduled maintenance requirements or a missed error, any downtime means potential lost revenue.
We take all our prospective customers through a Barcoding Discovery Session to identify any issues that will impact the design and implementation of a successful print and apply solution. That way we can be absolutely sure you get a system that is fit for purpose and built to work for your business.
Fill out the form below to book your Barcoding Discovery Session.